How to Improve Your Clarifier Treatment Process
In America there are thousands of wastewater treatment plants (WWTPs) – also referred to as sewage treatment plants. They range in size, from a municipal… read more
Mar 30, 2020
# of Minutes to Read
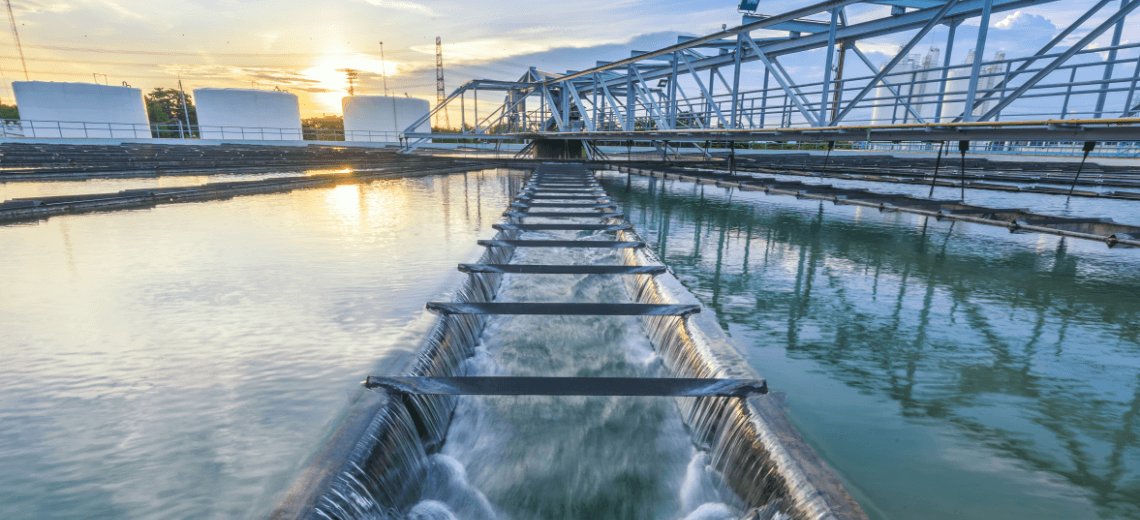
In America there are thousands of wastewater treatment plants (WWTPs) – also referred to as sewage treatment plants. They range in size, from a municipal wastewater plant treating the sewage for New York, to a small wastewater treatment system cleaning the water coming from a small factory.
In these plants, it’s the job of Plant Managers, Wastewater Directors and Wastewater Operators to effectively and safely treat waste water so any water discharged into the environment doesn’t contaminate it.
To do this, wastewater needs to go through various steps of treatment. These steps are typically clumped into primary, secondary, or tertiary treatment, but below is a brief overview of each step.
Step One: Bar Screening
The wastewater treatment process begins by removing large items from the influent that have entered the water through the sewer system. This removal prevents any damage from occurring to a plant’s treatment systems such as the pumps and valves. It also avoids the likelihood of the items blocking the flow of water.
Typically a bar screen is used. This will then be taken to a landfill.
Step Two: Screening
Step two of a Plant Manager’s water treatment methodology will be to flow the influent over or through a grit chamber in order to remove grit that isn’t caught in step one. Heavier grit falls to the bottom of the chamber so that the wastewater can flow to the next step of the treatment process.
Step Three: Primary Clarifier
The influent then flows into large primary clarifiers where heavy solids sink to the bottom. The speed of the water flow at this stage is crucial. Too fast and the solids won’t sink. Too slow and the process will be impacted up stream.
The solids that fall are known as ‘sludge’ and are pumped into a sludge digester, with the rate it settles a key indicator for how the machinery is working.
Step Four: Aeration
Air is then pumped into the tank to break down organic material, and help bacteria propagate and grow. Getting the right balance of bacteria is key, and another good indicator of whether onsite wastewater treatment is working.
Step Five: Secondary Clarifier
The treated wastewater is then pumped into a secondary clarifier. Again, the aim with the clarifier is for any very small solids to move to the bottom. These solids are called activated sludge and are formed of active bacteria.
By now the water has little organic material in it and should be nearing the required effluent regulations.
Step Six: Chlorination
Any remaining bacteria is then killed with the addition of chlorine. This disinfection means that any water which is discharged will not contain higher-than-allowed bacteria levels.
Step Seven: Testing
All WWTPs will need to test the water and activated sludge as it moves through the treatment plant’s process. However, at this specific stage a Plant Manager will analyze the water for (amongst other things) its pH, ammonia and chlorine levels.
Step Eight: Discharge
Once the water has gone through the above treatment process, and met the necessary regulations, it will be discharged into the environment.
What we’re going to focus on…
The purpose of this article is to zone in on clarifiers. Why? Because clarification is a vital component of pretty much all biological wastewater treatment systems.
However, while clarifiers are a great piece of equipment, they can be temperamental. They’re great for separating mixed liquor suspended solids (MLSS) but only if their density is different enough for the gravity to come into effect.
A clarifier’s performance depends on a number of factors:
- the characteristics of the activated sludge (its settleability)
- the hydraulic and solids loading rate
- the physical features of the clarifier itself
Three ways to improve your clarifier treatment process
1. Use coagulants to make larger floc.
Coagulants are chemicals used to help remove the color and cloudiness present in untreated, raw water.
They can be either organic or inorganic. The former are expensive so are only really used in plants where a low dose makes economic sense, while the latter are commonly used chemicals which rely on aluminium or iron.
By adding inorganic salts (such as aluminium or iron) to the water, charged particles are neutralised and suspended solids are destabilized. Flocculation then follows, with the neutralized particles colliding and coming together to form larger particles, also known as an agglomeration or ‘floc’.
Of course this process can occur naturally, but it can also be encouraged by adding polymeric flocculant aids. It’s best to do this when there is a high degree of turbidity in the water. When used with coagulants, sludge treatment, and filtration of clarified elements, flocculation will reduce water turbidity and remove color, solids and colloidal material from wastewater.
The end result of all of this is that flocs will settle more easily.
2. Reduce flow rate to the clarifier to give more settling time.
As mentioned above, it’s important to control the flow of liquid into the clarifier.
If you decrease the velocity then the hydraulic retention time inside the clarifier is increased. This reduces the likelihood of excessive turbulence and mixing, and so suspended particles can settle more effectively.
When sludge doesn’t settle properly the maximum solids loading rate diminishes. To reduce this rate, a Plant Manager can do a few things:
- Lower the sludge age by decreasing the mixed liquor suspended solids concentration.
- Lower the return activated sludge rate.
- Integrate more clarifiers into the treatment process.
- Artificially adjust the sludge volume index by adding a polymer or flocculent (see point one above)
Clarifiers have improved a lot in recent years, with specifically designed walls now added to promote flow uniformity. This decreases the chances of hydraulic instability and potential flow short-circuiting, and is obviously crucial given that a clarifier will be in near-constant operation. Reliability is key.
3. Maintain healthy bacteria
Wastewater treatment plants live and die by bacteria, and it’s the job of Plant Managers, Wastewater Directors and Wastewater Operators to maintain a healthy balance of it. ‘Good’ bacteria is needed to treat wastewater efficiently and safely, while ‘bad’ bacteria needs to be avoided as it could affect the running of the plant, and contaminate the environment if discharged.
Maintaining healthy bacteria levels will lead to the natural formation of flocs that settle.
Conversely, if small flocs are present then they will float in the clarifier and create a more turbid effluent. In order to reduce the chance of this happening you should reduce the sludge age.
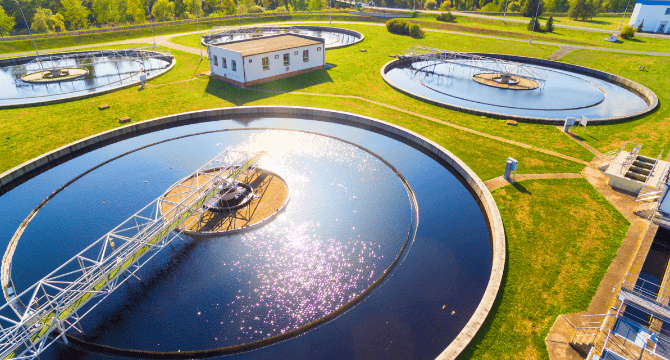
How do you know whether all of this is working?
Test, test, test!
If accidentally discharged from a treatment plant, contaminated water can have a devastating effect on fisheries, wildlife habitats, and our own health.
This is why Plant Managers – including both Wastewater Directors and Operators – are so anxious to ensure their treatment operations are safe, efficient, and compliant. To check this is the case, Plant Managers need to regularly test their water for bacteria levels and types.
Given the importance of this test, it’s wrong that current testing methods are expensive, resource-heavy, and time-consuming. The industry needs a better and simpler way to test the health of wastewater, and this is why we created opseyes.
With our AI-powered testing platform, sewage treatment plants can check the quality of their wastewater with just one photo. No test tubes. No Fedex. No sending sludge samples away to a lab for days. Just a simple-to-use platform and results with you in 10 minutes.
WWTPs can spot early warning signs of issues and get expert recommendations for what to do next… Do they need to renew bacteria levels every four days? Why is sludge not settling? Why are water tanks foaming?
The opseyes platform is perfect for quick testing and in emergencies, giving Plant Managers all the answers they need, when they need them.
What to learn more about AI and protect your treatment plant? Get in touch today.